Quality
Quality is
SuperFrio strength
Therefore, it has the best and most demanding companies and industries in the market as customers. We follow the methodology of standards of the management system as a guideline and we have results through the standardization of processes, efficiency, quality programs, innovation, indicators, continuous improvement, training and qualification of the team.
Q&SSMA
SuperFrio’s Quality, Health, Safety, Environment
and Social Responsibility Management System
SuperFrio’s Quality, Health, Safety, Environment and Social Responsibility Management System has as its basic premise the technical standards of the ISO series and is guided by an integrated policy.
In this way, the company can manage its operations in a systemic way, integrating all areas of the company. This allows us to demonstrate the commitment to the satisfaction of customers, employees and shareholders.
Management is focused on compliance with applicable legal requirements and flexibility of adaptation to specific processes and requirements of customers.
In addition, SuperFrio works on several projects and initiatives for continuous improvement and energy efficiency, aiming at the preservation of the environment, the quality and safety of the products it moves and the health and safety of its employees.
The operating units have registration in the Federal Inspection Service (SIF) and National Registry of Seeds and Seedlings (RENASEM), ensuring excellence in the quality of warehouses and enabling greater business opportunities for customers.
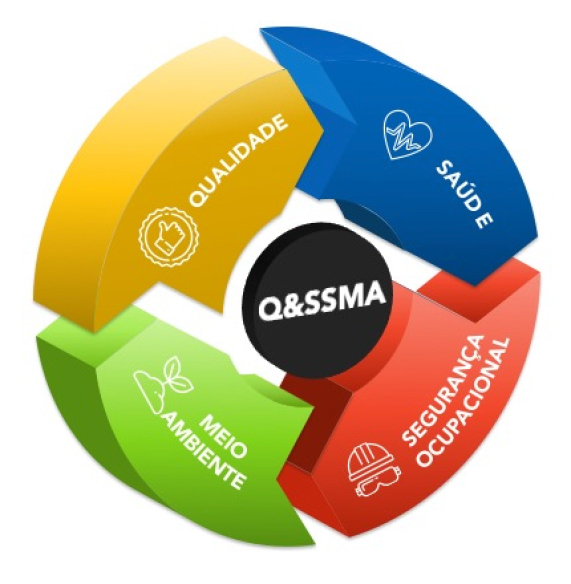
Inspections of products, vehicles
and standardization
of operations
Temperature control
of receiving and
shipping operations
Strict control and
monitoring of
temperature and humidity
Food safety
HACCP Program (Hazard Analysis and Critical Control Point)
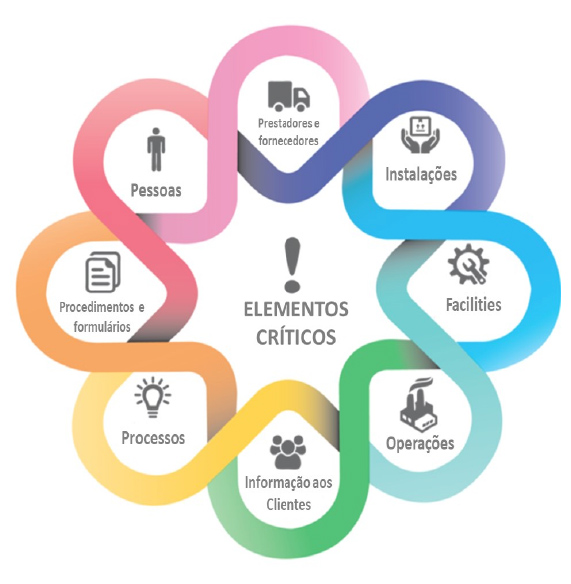
The HACCP (Hazard Analysis and Critical Control Point) program is integrated into the Quality Management System, which aims to ensure product safety, which is based on the requirements of FSSC 22000 and BRC standards, both recognized by the Global Food Safety Initiative (GFSI).
An effective process of a food safety system implies prior compliance with prerequisite programs followed by the analysis and identification of the possible risks of contamination and hazards inherent to the products. Then a detailed plan is established with preventive control measures for the effective implementation of the system, and continuous improvement is carried out through monitoring and verification by the Food Safety Team and Operational Committees.
We invest in the assistance of qualified consulting that has high knowledge and innovation to achieve continuous improvement, through the development of prerequisite programs, new processes and flows in order to meet the current food safety standards.
We value the training and qualification of our team ensuring all internal procedures implemented, aiming to maintain quality, safety and standardization in all activities carried out by SuperFrio, as well as the satisfaction and protection of the brand of our customers.
Process management
and critical
analysis of results
Training and capacity
building of the entire team
Monitoring and verification of operations ensuring safe food to consumers and protecting customers’ brand
Cold quality
Our facilities are equipped with the best in refrigeration equipment, ensuring compliance with the temperature requirements of frozen, cold and air-conditioned products through the storage chambers, preserving the quality according to current standards and customer expectations.
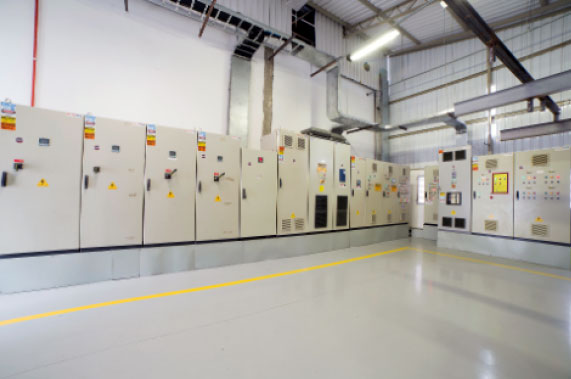
Our machine rooms are sized to meet
the proper cold generation and we
have high quality equipment and technology
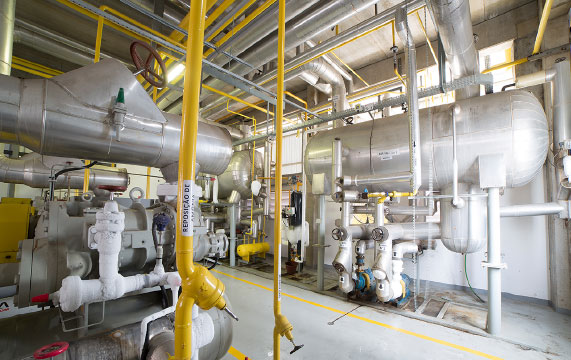
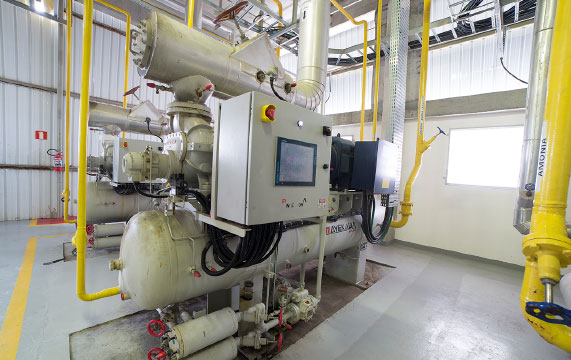
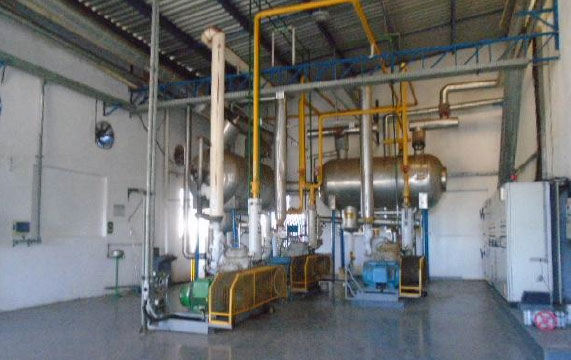
Information technology
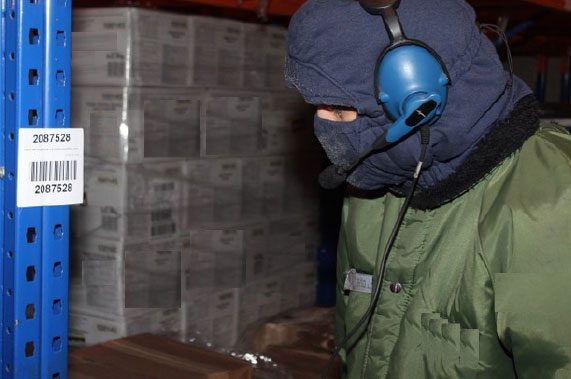
SuperFrio uses the most advanced information technology, with cutting edge infrastructure and one of the best warehouse operations management software in the world: WMS JDA.
It is a pioneer in Picking By Voice technology in freezing temperatures in Brazil. It has a mesh and an efficient fractional distribution management system, integrated with ERP, TMS and customer systems. All this enables visibility, management and real-time tracking of information about inventory, status and performance of operations and deliveries.
Automated
engine rooms
WMS system
with collectors
Online access by the
client for data query